The meteoric rise of Broadleys Bagpipes – Part 1
Broadleys could be the most successful bagpipe and reed maker you’ve never heard of.
In the ultra-risk-averse world of piping and drumming, getting a Grade 1 band to compete with your pipe chanter can take years or even decades. Far more often than not, it never happens.
After only six months, Ross Watson, founder of Broadleys Bagpipes & Reeds in Kirkcaldy, Scotland, heard his pipe chanters played by a full band for the first time.
![Simon Fraser University playing Broadleys chanters on stage 2023.[Photo Alister Sinclair]](https://www.pipesdrums.com/storage/2023/08/SFU_Generations_Concert_2023-48.jpg)
Like almost every bagpipe or reed maker, Watson learned his craft with another company. He was an employee of Shepherd Bagpipes for some 28 years, recruited by Bob Shepherd himself when Watson was learning the carpenter/joiner trade. At 17 years old, the great Shepherd approached him to apply his skills to bagpipe making with R.T. Shepherd & Son.
Watson’s first teacher was Jock Innes, and his first band was Kelty & Blairadam. He would go on to play with the Grade 1 Dysart & Dundonald in the late 1990s, but a crushing injury to his birl finger put paid to his competitive piping career.
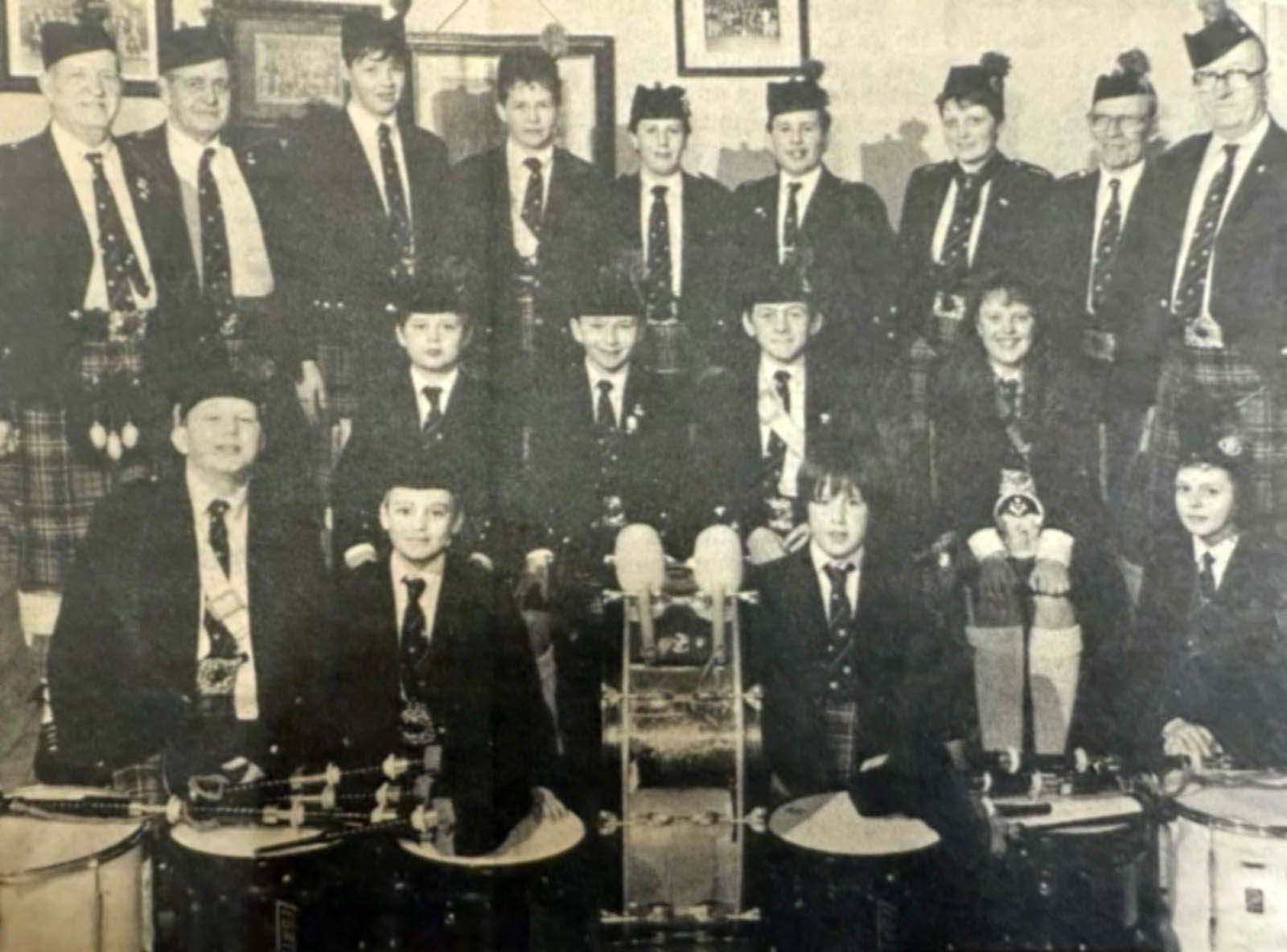
Over his decades of work with Shepherd Bagpipes, he saw Shepherd pipe chanters become one of the most successful throughout the grades.
Top-grade bands still use “vintage” Shepherd chanters from the 1990s. After decades and hundreds, if not thousands, of practices and contests and the inevitable carving of holes, opening reed seats, and occasional mishaps, demand for replacement chanters has grown strong.
Over the pandemic, Watson decided to take the plunge after seeing an old farmhouse holding for sale in Kirkcaldy. He had grown up around the same kinds of buildings, and the nostalgia was irresistible.
The farm’s name was “Broadleys.”
The building and its grounds were in disrepair, but renovations restored them to the condition needed to be a rustic bagpipe workshop.
Rather than taking a more predictable route of naming his bagpipe-making business after himself, Watson decided “Broadleys” was more faithful to his personality as someone who prefers to be behind the scenes.
Indeed, Ross Watson is humble and reserved. He understands the value of publicity but prefers to let his products do the talking.
The uptake of Broadleys “Legacy” and “Trad X” chanters includes not only SFU but also Shotts & Dykehead Caledonia and Police Scotland Fife, bands that need instruments to supplement an existing set of older Shepherd chanters.
Watson turns his chanters by hand, preferring traditional methods over laser-guided Computer Numerical Control (CNC) machines. He’s not limited to Highland pipes. Smallpipes and practice chanters are always ready to be made to order.
So far, he has managed to keep up with manufacturing mostly on his own, with some part-time help and the assistance of his daughter and wife in managing administrative and accounting tasks.
Ross Watson stresses that his family and friends have contributed significantly to the start of Broadleys Bagpipes & Reeds. Encouraging him to start the business, he says, helped him have confidence that he was doing the correct thing. He says their help was massive.
We connected with Ross Watson to learn how Broadleys Bagpipes & Reeds has become such a success in such a short time.
Here’s the text of our discussion, edited for clarity.
pipes|drums: Tell us about Broadleys Bagpipes and how it all got started.
Ross Watson: I was in the industry for about 28 years. I thought, right, I’ll try to make a new venture and start up a bagpipe business. And going by what I knew, I thought I would take that forward and see how I got on going into the market with everything and see where it would take me.
p|d: It can take a while for pipe chanters to catch on, but yours have caught on really quickly, relatively speaking. Did you ever think it would happen that way?
RW: No, I didn’t. I thought, right, I’ve just had to see how it goes. And going by what I know, I would just put that into production. To put the Broadleys name out there and see how the product is going to react to the market.
Also, working closely with pipe-majors and stuff about what they’re looking for and the knowledge of what I know, and just put that into the equation to come up with the products that were going to be settled on.
p|d: Did you go into the business with any short- or long-term goals in mind? Or was it simply “Let’s see where things go”?
RW: Short-term was to basically get the products out there, and get people to look at the products and try them, and hopefully they like what they heard. And then that be a stepping-stone for the long-term side of things. On Monday [January 27th], it’s two years from the day that the business started. I don’t know whether that’s short-term or long-term, but just keep doing what we’re doing, and hopefully the long-term, I’ll just keep continuing on the way it’s going and be a success.
p|d: If you think back, maybe 30 or 40 years ago, only a handful of bagpipe makers had chanters that caught on. If you look at the market now, there are a lot more. Have you ever had concerns about whether there was going to be enough space in the market to add another maker?
RW: Yeah, it was a big concern because there are a lot of excellent manufacturers out there doing everything and different things: reeds, chanters, bagpipes, everything, smallpipes, the lot. So, yeah, it was a serious worry for me. But I just put into what I knew, and I’ve put a lot of my years into manufacturing products. I just put that out there and just hope that that would be enough to take things forward for me in the business, and that’s what people would like.
So, yeah, that was a worry, and it still is, because we’re all in there to really put our products out there and get them to be successful.
p|d: And you chose right from the beginning to go with hand-turning?
RW: Well, I’m old school, if you want to call it that, but a traditionalist, I thought, right, and, and that’s what I’ve been doing for a long time as well, making pipes in my hands. And you get, you get to, you get to like it. You get to like what you’re doing with the wood. You’re looking at different parts of the wood all the time. It’s in your hands from start to finish. And so, yeah, it’s just how I choose to do it. And you’re just sort of loving that sort of product as you’re actually working with it. And every single piece is different.
You feel that from all the way through the process. That’s when I chose to do that. But the market is, and there’s quite a big sigh out for bagpipes. And there’s quite a lot to get out there, and making them traditionally by hand takes quite a lot of time. I could understand that CNC must come into the equation to meet the demand. But that’s that’s what I’ve done from day one. I’ve not as yet stepped into that side of things.
p|d: Let’s return in Part 2 and talk about the uptake your instruments have had cracking the Grade 1 market. Stay tuned for part two of our conversation with Ross Watson of Broadleys Bagpipes, coming soon.
I would love to know what is the design pitch of these new chanters….and, more esoteric,…what makes these so suddenly grandly different…outstanding…among existing several other new or older
chanters typically played by the top bands?